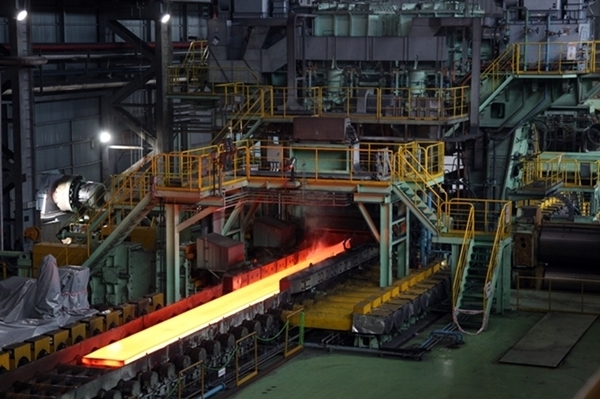
◆차가운 스틸이 생명을 살린다
환자들이 위생적으로 의료 치료를 받을 수 있게 된 것은 1913년, 스테인리스 스틸(써지컬 스틸)의 발명 이후다. 이전엔 비위생적인 환경에서 수술을 받다가 세균 등에 감염이 되어 많은 사람이 목숨을 잃었다.
세계보건기구(WHO) 역시 현대 의료 서비스의 가장 심각한 난제 중 하나로 치료 도중에 환자들이 감염되는 문제를 꼽기도 했다. 전 세계적으로 매년 수억 명의 환자들이 감염으로 인한 질환에 노출되고 있기 때문에 병원에서 위생적인 환경을 조성하는 것이 무엇보다 중요하다는 것이다.
2010년 WHO에서 발표한 자료에 따르면 고소득 국가에서는 중환자실 환자들의 약 30%가 감염에 시달리며, 저소득 국가에서는 그보다 2~3배 많은 감염 환자가 발생하는 것으로 나타났다.
이러한 상황에 의료용 스테인리스 스틸인 써지컬 스틸은 녹슬지 않는 고유 성질인 ‘내부식성’을 갖고 있어 부식될 염려가 없고, 다른 어떠한 부작용 없이 안전하게 살균 처리가 가능한 특장점을 통해 많은 환자의 목숨을 지켰다.
수술용 메스나 주삿바늘, 부러진 뼈를 고정하는 나사처럼 신체 부위에 직접 닿거나 체내에 들어가도 안전한 덕분에 전 세계 병원에서는 스테인리스 스틸을 사용하고 있다. 만약 써지컬 스틸을 사용하지 않는다면 파상풍에 걸리거나 각종 세균에 감염될 우려가 있다.
특히 오래 써도 새것과 차이 없는 써지컬 스틸의 살균력은 특기할만하다.
2017년 국제스테인리스강협회(ISSF)의 ‘스테인리스 스틸의 살균력 연구’에 참여한 영국 메트로폴리탄대학교와 프랑스 아그로파리테크 그라제콜의 연구진은 오염 스테인리스 스틸과 새로운 스테인리스 스틸을 식중독과 감염을 일으키는 ‘황색포도상구균’과 저항력이 강해 치료하기 어려운 ‘녹농균’에 동시에 노출했다.
이후 얼마간의 시간이 흐른 뒤 두 스틸을 동일한 살균제로 소독했을 때 두 샘플 모두 황색포도상구균은 99.9%, 녹농균은 97.6% 멸균된 것으로 나타났다. 이 실험을 통해 의료용 스틸이 오랜 시간이 지나도 위생적으로 안전하게 사용할 수 있다는 것이 재확인된 셈이다.
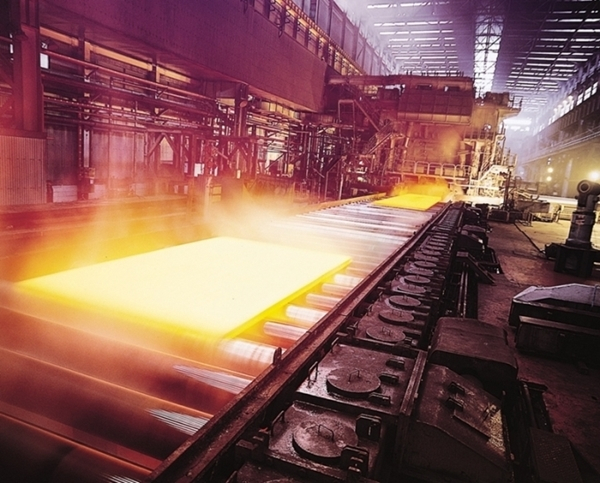
해상풍력은 바다에 풍력발전기를 설치하고 그곳에서 부는 바람의 운동에너지를 변환해 전기를 얻는 발전 방식이다.
대형 풍력발전기의 경우, 블레이드(날개)가 한 바퀴 회전하는 것으로 일반 가정에서 29시간 동안 사용할 수 있는 전력을 생산해낸다.
특히 해상풍력은 육상풍력에 비해 입지 제약으로부터 자유롭고 높은 효율로 에너지를 생산할 수 있어 전 세계적으로 확대되는 추세다. 한국도 전남 신안 앞바다에 2028년까지 11조 원을 투입하는 해상풍력 단지를 조성 중이다.
해상풍력 단지에 구축되는 풍력발전기는 크게 보면 지지대 역할인 ‘타워’와 바람을 맞고 회전하는 ‘블레이드’, 겉으로는 보이지 않지만, 에너지를 생성해내는 ‘발전기’와 타워를 해저에 단단히 고정하는 역할을 하는 ‘하부구조물’로 구성됐다.
이중 타워와 하부구조물은 바다 한가운데서 바람을 맞는 가혹한 환경과 저온 충격에도 20년 이상 변형 없이 버틸 수 있는 소재로 제작돼야 한다.
이에 따라 구조물용 ‘저온인성보증강’ 등 스틸(철강)은 풍력발전기에 가장 많이 쓰이는 소재다. 최근 발전기가 대형화되면서부터 타워와 하부구조물에 ‘대단중(大單重)강’도 많이 쓰이고 있다.
해상풍력기 1기당 약 1500톤에서 2300톤(8~9MW급 기준)의 철강재가 쓰이며, 2020년 기준 세계적으로 연간 100만 톤이 넘는 해상풍력발전용 철강 수요가 발생할 전망이다.
이러한 상황에 글로벌 1위 철강사 포스코는 풍력발전기에 특화된 고급 강종의 생산능력을 꾸준히 확대하고 있다. 현재 육상과 해상을 통틀어 전 세계 풍력발전기 10대 중 1대는 포스코 스틸로 만들어지고 있다.
특히 회사는 세계 최대 규모로 조성 중인 해상풍력발전 단지인 영국의 혼시(Hornsea) 프로젝트에 들어가는 철강재의 약 30%를 공급하며 유럽 그린 에너지 시장에서 뚜렷한 두각을 드러내고 있다.
포스코는 이와 관련해 “영국뿐만 아니라 대만과 큰 성장이 예상되는 미국, 베트남 등의 시장에서도 메인 공급사 자리를 꿰차기 위해 선제 마케팅 활동을 활발히 전개 중”이라며 “그린에너지 시대, 바다 한가운데 부는 바람 속에도 포스코 스틸이 있던 셈”이라고 전했다.
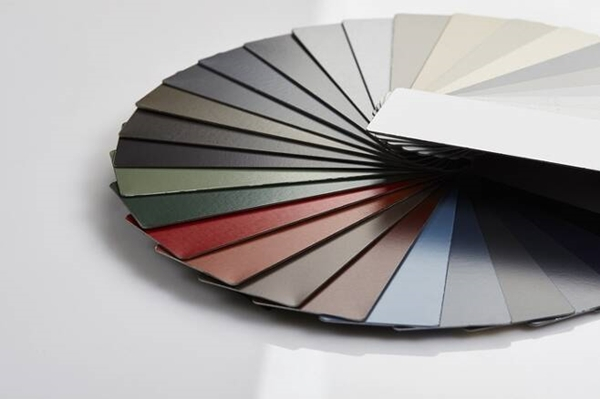
“기름 한 방울 나지 않는 나라.” 대한민국을 묘사할 때 쉽게 하는 말이다. 여전히 한국에서는 기름이 솟아나진 않지만 지금 세계 곳곳의 자원을 탐사하고, 생산하고, 운반하는 일에는 대한민국의 힘이 쓰이고 있다.
그 주인공은 세계 3위 에너지 수입국 인도에서 에너지를 내륙으로 수송하는 관로다. 관로는 파이프라인이라는 이름으로 주로 불린다. 원유는 인도 수입의 제1품목이다. 수입되는 에너지 자원들은 해상운송을 거쳐 항만의 터미널로 들여오고, 이를 내륙으로 수송하는 것이 파이프라인의 역할이다.
인도에서는 신규 파이프라인 건설이 한창 진행 중인데, ‘기회의 땅’ 답게 파이프라인 프로젝트로만 연간 60만 톤 이상의 철강 수요가 창출되고 있다.
그러나 이 시장이 누구에게나 활짝 열려있는 것은 아니다. 인도 정부는 무역 장벽을 계속 높이고 있고 파이프라인 프로젝트의 발주처들은 강관사로 하여금 일정 비율의 철강 소재를 로컬재로 사용할 것을 강제하고 있다. 때문에 남은 물량을 가지고 수입재끼리 치열하게 경쟁해야 하는 구조라는 게 업계 평가다.
지난해에는 인도국영석유공사 IOCL(Indian Oil Corp. Ltd)이 2건의 대형 프로젝트를 발주했다. 1차로 동부 지역의 Barauni부터 Haldia를 잇는 프로젝트, 2차로 남부 Ennore부터 Tuticorin을 잇는 프로젝트가 연달아 터졌다. 수입되는 원유와 가스를 내륙으로 운송하는 파이프라인을 건설하는 것이다.
프로젝트에는 총 강재 소요량 20만 톤 이상, 강종 역시 ‘고급강종’이었다. 글로벌 철강사들이 입찰에 열을 올렸는데, 이 중 70%의 철강재는 대한민국의 포항과 광양에서 만들어졌다. 철강 맏형 포스코가 수입재로는 유일하게 메인 공급사 자리를 거머쥐며 활약한 것이다.
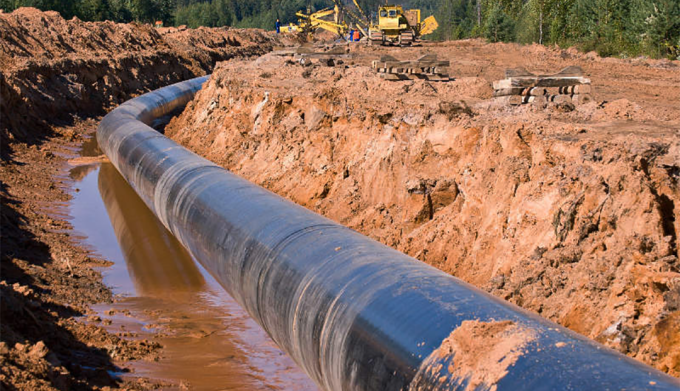
그러나 2000년대에 들어 수압파쇄 및 수평시추 기술이 상용화되며 신에너지원으로 급부상했다. 특히 미국에서 줄줄이 셰일가스전이 개발됐고 이는 미국을 전 세계 ‘제1 산유국’으로 만들어주기도 했다.
때문에 미국에서는 자연스럽게 신규 파이프라인 설치도 활발해졌다. 2018년에는 미국 최대의 유전지대인 Permain Basin의 셰일가스를 운송하기 위해 Texas Waha에서 Agua Dulce까지 약 700km 구간을 잇는 파이프라인 건설 프로젝트가 추진됐다. 프로젝트 명은 Gulf Coast Express(이하 GCX) 파이프라인 프로젝트다. 지난해 가동되는 파이프라인 중 최대 규모였다.
프로젝트에 소요되는 강재량이 30만 톤에 육박하다 보니, 아르셀로미탈, 일본제철, JFE 등 다수의 글로벌 철강사가 경쟁을 치렀다. 하지만 트럼프 정부의 거센 무역 보호 조치로 인해 철강재를 전량 미국 로컬재로 사용하는 것이 논의될 만큼 수입재의 진입장벽은 높았다.
특히 한국 철강재의 경우 당시 높은 관세로 인해 사실상 미국으로의 직수출이 불가능했다. 하지만 이 프로젝트에서도 전체 물량 3분의 1에 해당하는 강재를 포스코가 공급하며 높은 무역 장벽을 뛰어넘는 포스코 초프리미엄 제품의 저력을 보여줬다.
이는 프로젝트에 참여한 터키의 강관사 BMB(Borusan Mannesmann Boru)가 공급안정성과 원가절감 등을 이유로 수입재를 사용하는 가능성을 열어두고 있었기 때문이다.
파이프는 강재를 가져다가 다시 한번 가공해 만들기 때문에, 철강사와 강관사의 파트너십이 제품 품질에 큰 영향을 미친다. 포스코는 터키에 있는 BMB 공장을 찾아 적극적인 솔루션 마케팅을 펼쳤다. 혹시 모를 품질 리스크를 없애고자 BMB의 설비를 함께 점검하고 개선이 필요한 부분은 솔루션을 제공했다.
또 생산 과정 중에는 2개월간 프로젝트의 검사관이 강재 생산 과정을 직접 확인할 수 있도록 제철소 현장에서 입회를 지원했다. 강재 공급 후 애프터서비스에 대해서도 그간의 경험치를 바탕으로 자신 있게 약속했다.
결국 BMB는 당초 고려했던 물량보다 더 많은 양을 포스코에 주문하기로 결정했다. 강종은 전량 포스코의 월드톱프리미엄 제품이었다. 이후 포스코 강재는 2018년 5월부터 10월까지 6개월에 걸쳐 공급 완료됐고, 강재로 만들어진 파이프라인은 2019년 9월부터 가동에 들어갔다.
GCX 파이프라인은 하루에 약 20억 입방피트(ft3, Cubic feet)의 천연가스를 운송하며, 일부는 멕시코만에 위치한 LNG 액화기지(Liquefaction Plant)를 통해 LNG로, 일부는 천연가스 형태로 멕시코 등으로 수출되고 있다.
킨더모건(Kinder Morgan)은 이번 GCX 프로젝트 외에도 하이웨이 파이프라인(Permian Highway)도 파이프라인을 건설 중이며, 추가적인 프로젝트도 고려 중인 것으로 알려져 있다. 포스코는 올해도 전 세계 파이프라인 프로젝트를 면밀히 주시하며 글로벌 마케팅 활동을 이어나갈 예정이다.
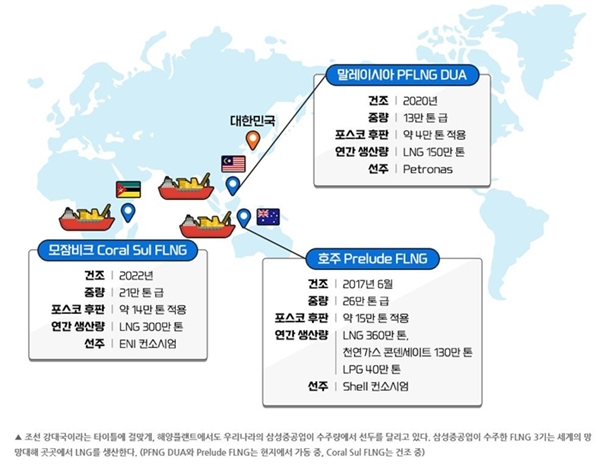
“배가 아니다. 기름 나는 섬이다.” 생긴 것은 영락없는 배지만 실은 바다 위에 떠 있는 에너지 플랜트, FPSO(Floating Production Storage and Off-loading)를 두고 하는 말이다.
FPSO는 한 곳에 20~30년간 머물면서 해저의 원유를 생산하고 저장, 하역한다. 같은 용도이지만 원유가 아닌 가스를 생산하는 설비는 LNG-FPSO, 줄여서 FLNG(Floating LNG)이라고 부른다.
FPSO는 자기 힘으로 항해하지 않고, 최초 유전이 있는 장소로 이동할 때도 예인선에 이끌려 이동을 한다. 그래서 업계에서는 이를 선박보다는 플랜트로 구분하며, 최첨단 과학을 총집결한 해상 복합 구조물로 평가한다.
세계 곳곳에서 발주되는 FLNG를 독점하고 있는 나라는 다름 아닌 조선 강대국 대한민국. 그중에서도 삼성중공업은 2010년 이래 전 세계에 발주된 4기의 초대형 FLNG 중 3기를 수주하면서 해양 지존의 입지를 단단히 다졌다.
현재 삼성중공업 거제조선소에서는 ‘모잠비크 코랄 술(Coral Sul) FLNG’를 한창 건조 중이다. 길이 439미터, 폭 65미터, 높이 38.5미터로 자체 중량 21만 톤 급의 초대형 해양 설비다.
정규 축구장(길이 105미터, 폭 68미터) 4개가 나란히 들어갈 정도라고 하니, 그 크기가 어느 정도일지 가늠이 될 것이다. 사업규모도 삼성중공업이 수행하는 공사 금액만 2조8534억원(약 25억 달러) 정도다. 모든 면에서 ‘초대형’ 프로젝트다. 이 프로젝트 이전에 건조한 로열더치쉘의 ‘프렐류드(Prelude) FLNG’는 세계에서 가장 큰 FLNG로도 기록됐다.
여기서 주목할 대목은 이 어마어마한 플랜트에 들어가는 후판 전량을 이례적으로 단일 철강사가 공급했다는 사실이다.
조선사는 주로 대형 프로젝트에 들어가는 철강재의 공급사를 다원화하는 전략을 펼친다. 원가 절감도 꾀하고, 앞서 언급한 공급 안정성 측면에서도 더 안전하다고 믿어서다.
그럼에도 불구하고 삼성중공업은 프렐류드 FLNG의 후판 15만 톤 그리고 현재 건조 중인 코랄 FLNG의 후판 14만 톤까지 전량을 포스코에 맡겼다.
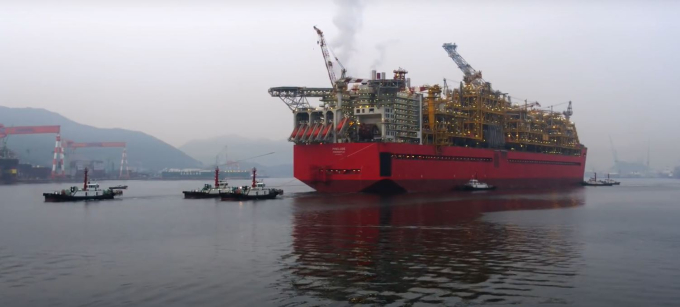
페트로나스의 FLNG의 경우 PFLNG DUA으로 명명식을 가지고 지난 2월 18일 출항했다.
PELNG 두아(PFLNG DUA)는 말레이시아 동부 코타키나발루 해안에서 140km 떨어진 로탄 가스전 위에 계류한다. 앞으로 20년간 매년 LNG 150만 톤을 생산할 예정이다. 현재 건조 중인 모잠비크 코랄 FLNG도 건조가 완료되면 아프리카 대륙까지 건너가 2020년부터 연간 300만 톤의 LNG를 생산해내며 지구촌의 불을 밝힐 것이다.
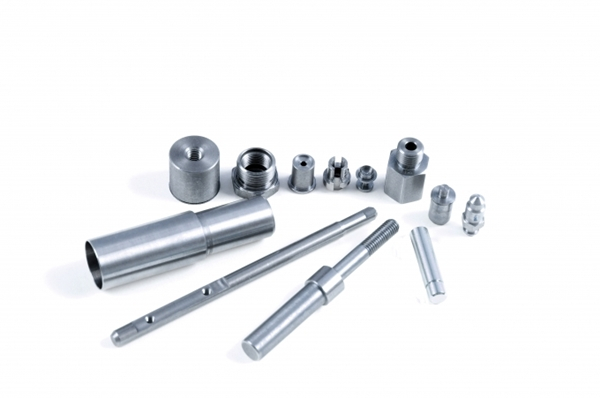
철강 맏형 포스코가 세계 최초로 친환경 흑연 쾌삭강(PosGRAM, GRAphitic steel for Machinability)의 양산제품 개발에 성공하고 판매확대에 본격 나섰다. 쾌삭강은 본래 일본 등 해외 전량 수입에 의존하던 소재로 국산화를 통해 국가 산업 경쟁력 제고에 도움이 될 전망이다.
포스코가 개발한 쾌삭강은 단면이 원형이며 가늘고 긴 철강재인 선재 제품의 하나로, 절삭 면이 깨끗하고 빠르게 잘리는 강이다. 주로 복잡한 형상이나 치수 정밀도가 중요한 자동차, 전기·전자 및 사무자동화 기기의 정밀 부품 제작에 사용된다.
기존 쾌삭강에는 절삭성 향상을 위해 납을 첨가했는데, 납은 제품의 생산, 가공, 재활용 처리 시 마이크로미터(㎛) 크기의 미세 입자로 공기 중에 퍼져나가 작업자에게 염증이나 신경계 손상 등의 부작용을 유발할 수 있다.
이에 따라 유해물질 제한 국제 지침인 RoHS와 ELV에서는 제품 내 납 함유량을 최대 0.1%로 규정하고 있는데 대체 소재가 없는 납 쾌삭강만은 별도의 예외 규정을 두고 최대 0.35%까지 허용하고 있다.
그러나 글로벌 기업을 중심으로 납이 함유된 부품 사용을 금지하는 추세가 확대되고 있으며, 납사용을 규제하는 지침 역시 강화될 것으로 보인다.
포스코의 이번 흑연 쾌삭강 개발은 친환경 소재인 흑연을 활용해 납쾌삭강 이상의 우수한 절삭성을 확보한 데에 큰 의의가 있다는 평가다. 열처리를 통해 구현한 균질한 조직은 어느 방향으로 절삭을 하든 균일한 절삭성을 나타내 가공 효율이 한층 더 높아질 수 있게 됐다.
또 주변 자기장에 쉽게 자석화되는 특성 덕분에 솔레노이드 밸브와 같은 정밀제어 부품으로 사용하기에도 적합하다. 솔레노이드 밸브는 원통형으로 감은 전기 코일(솔레노이드)에 전기를 흘려 발생하는 전자기력으로 쇠막대(플런저 plunger)를 움직여 구동하는 밸브다. 쾌삭강은 플런저 소재로 사용된다.
포스코는 앞서 2017년 흑연 입자의 분포 및 제어 기술의 개발을 시작으로 쾌삭강 개발에 착수했으며, 지난해 생산 라인에서 양산 제조기준을 정립하며 개발을 완료했다.
현재 쾌삭강 시장은 세계적으로 연간 100만톤 규모로 추정되는데 이중 납을 함유한 제품의 비율이 절반을 넘는다.
국내에는 납쾌삭강을 생산하는 업체가 없어 연간 2만3000여톤을 일본 등 해외에서 전량 수입해 오고 있는데, 포스코는 PosGRAM 양산으로 수입에 의존하던 쾌삭강의 상당 부분을 대체해 소재 독립에 도움이 될 전망이다.
im9181@kukinews.com