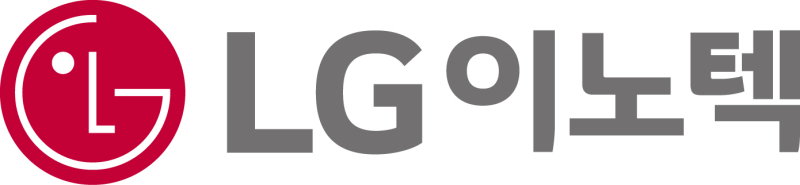
LG이노텍이 사업 경쟁력 강화를 위한 디지털 전환을 가속화한다.
8일 LG이노텍은 글로벌 1위 엔지니어링 시뮬레이션 기업인 앤시스와 손잡고, ‘디지털트윈’ 기술을 전 공정으로 확대 적용해 나가겠다고 8일 밝혔다.
디지털트윈은 가상공간에 사물을 똑같이 복제하여, 현실에서 발생할 수 있는 상황을 컴퓨터로 시뮬레이션해 결과를 예측하는 기술이다. 다양한 산업과 사회 문제를 해결할 수 있는 기술로 주목받고 있다. 특히 제품 개발시간과 비용을 줄일 수 있어 제조업에서 도입이 빠르게 늘고 있다.
앤시스는 3D 모델링, 인공지능, 머신러닝 등을 활용한 시뮬레이션 분야에서 세계 최고 수준의 기술력과 구축 경험을 보유하고 있는 것으로 알려져 있다. 이번 협력으로 LG이노텍은 앤시스의 최신 디지털 트윈 솔루션과 시뮬레이션 소프트웨어를 활용하여 글로벌 최고 수준의 디지털 트윈 환경을 구축할 수 있게 됐다.
LG이노텍은 앤시스와 함께 일부 개발과 생산 공정에 디지털트윈을 시범 적용하여 가시적 성과를 거두고 있다. 향후 차량 커넥티비티, 센싱 등 자율주행 부품을 비롯한 전 제품군의 개발 및 생산 공정으로 디지털 트윈을 본격 확대해 나간다는 계획이다.
특히 LG이노텍은 현재 연구개발 분야에서 디지털트윈을 활용, 높은 효과를 보고 있다. 가상 환경에서 설계 검증을 진행하고, 그 데이터를 바탕으로 실제 실험 횟수와 시간을 최소화한 것이다.
반도체용 패키지 서브스트레이트(PS) 제품 개발에 디지털트윈을 적용해 개발 기간을 99%까지 줄였다. 기판은 제조 과정에서 가해지는 열과 압력 등으로 인한 ‘휨’ 현상을 최소화하는 것이 중요하다. 이를 위해 회로 설계 구조, 물질 성분비 등의 조합을 최적화하는 시뮬레이션 과정을 거친다. LG이노텍은 3D 모델링을 통한 가상 시뮬레이션으로 기판 1개의 휨 정도를 예측하는 시간을 기존 11일에서 3.6시간으로 단축시켰다.
디지털트윈은 FC-BGA(플립칩 볼그레이드 어레이) 생산 공정에도 적용됐다. 디지털트윈을 통해 FC-BGA 공정 설비를 최적의 조건으로 세팅하여, 램프업(양산 초기 수율 향상을 통한 생산능력 확대) 기간을 절반으로 단축하는 데 성공했다. 이와 함께 전장부품 생산 공정에도 디지털트윈을 적용, 생산성을 기존 대비 40% 높인다는 계획이다.
LG이노텍은 차량 통신모듈, 라이다(LiDAR) 등 신성장 사업을 포함한 전 제품군의 개발·공정으로 디지털트윈을 빠르게 확대해 나간다는 방침이다.
노승원 CTO(전무)는 “LG이노텍이 그리는 미래는 가상 공간을 통한 시뮬레이션 결과를 물리적 생산 시설과 연동해 실제 생산까지 자동으로 이어지는 ‘메타 매뉴팩처링’”이라며 “이를 위해 R&D, 생산, 품질관리 등 전 밸류체인에 고도화된 디지털 트윈을 빠르게 접목해 차별적 고객 가치를 만들어 나갈 것”이라고 말했다.